Understanding Parenteral Vial Capping Optimization
One of the most important aspects for choosing a packaging system for parenteral vial drug products is to ensure an ideal fit between all components. In addition to characterizing the quality of selected components, parenteral vial capping optimization programs at ZebraSCI have added benefits to minimize risk down the road.
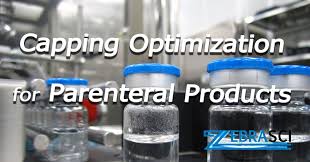
Assurance of package integrity originates from the use of appropriate materials, accurate and optimum closing properties, proper dimensional fit and consistent control of processes used to assemble the closed package. There are several types of studies recommended to be conducted during development of the container closure system (CCS) and to support filling, final assembly operations and ensure adequate seal quality throughout the product life cycle.
Component Quality for Vial Capping Optimization
Selected component materials each have critical dimensional tolerances. Component geometry directly affects the inherent and intended integrity of the final packaged drug product. Component variables critical to success include but are not limited to:
Vial Flange Thickness Stopper Flange Thickness Alu Seal Skirt Length
Vial Inside Neck Diameter Vial Inside Neck Geometry
Stopper Plug Diameter Stopper Plug Geometry
To assist clients with determining the quality of selected components, ZebraSCI has numerous non-contact vision measurement technologies available. Our semi-automated systems offer precise measurements and allow us to quickly give you an overview of lot-to-lot variability and bin parts at low, nominal and high specification.
Additional Studies for Optimization of Vial Capping
The next step in the process involves percent compression analysis to understand the component stacking variation. There is an optimum window of closure compression that is critical to seal quality. Poor compression cannot be visually detected and can lead to loss of integrity. Too much compression can lead to glass breakage, dimpling or bulging of stoppers and various other issues that negatively impact the drug product packaging process.
Analyzing the relationship between compression and residual seal force (RSF) provides additional insight. (RSF) is the measured stress the compressed rubber closure flange continues to exert on the vial-sealing surface after application (crimping) of an aluminum ferrule. By correlating RSF to percent compression, RSF can then be used as an indirect test method to estimate closely the elastomeric closure compression and can be further used as a predictor of leakage risk.
By correlating RSF measurements with corresponding leak rates via a container closure integrity (CCI) method such as helium leak detection or headspace gas analysis, RSF can be used to effectively evaluate initial and continued sealing of a vial system.